


%30-50
CAPACITY INCREASE
%50–80 WATER SAVING
%50–80 STEAM SAVING
%30–50 ELECTRICITY SAVING
LESS PEELING
HIGHER FASTNESS



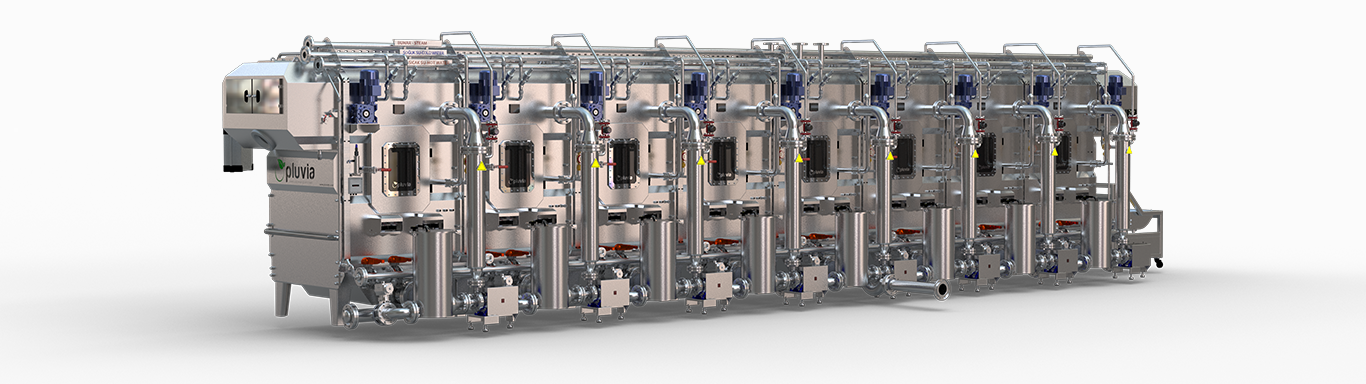
When the washing steps in the dyeing process is carried out with Pluvia, total dyeing process is shortened by 3 hours. Around 40% capacity increase is achieved.
Water consumption of Pluvia is 7-10 lt/kg. Conventional dyeing machines consume 30-50 lt/kg water.
Steam consumption of Pluvia is 0,5 kg/kg. Conventional dyeing machines consume 2-3 kg/kg steam.
Electricity consumption of Pluvia is 0,03 kW/kg. Conventional dyeing machines consume 0,06 - 0,1 kW/kg.
Pluvia washing speed 35-50 mpm. There is no peeling, no elongation. With conventional dyeing machines, the fabric speed is around 300-450 mpm which causes mechanical wear on the fabric.
Pluvia effectively washes by penetrating water through fabric. Hence, the washing fastnesses value increases. With conventional dyeing machines the fabric passes only once with 300-450 mpm speed through nozzle in every 2-3 minutes in dyeing machine.
PLUVIA CIRCUM CONSUMPTIONS | |||
WASHING AFTER DYEING | WASHING AFTER PRINTING | WASHING YARN DYED FABRICS | |
Water Consumption | 7 - 10 l/kg | 20 - 30 l/kg | 5 - 7 l/kg |
Steam Consumption | 0,25 - 0,35 kg/kg | 1,5 - 2,5 kg/kg | 0,1 - 0,25 kg/kg |
Electricity Consumption | 0,03 - 0,07 kW/kg | 0,06 - 0,10 kW/kg | 0,02 - 0,05 kW/kg |