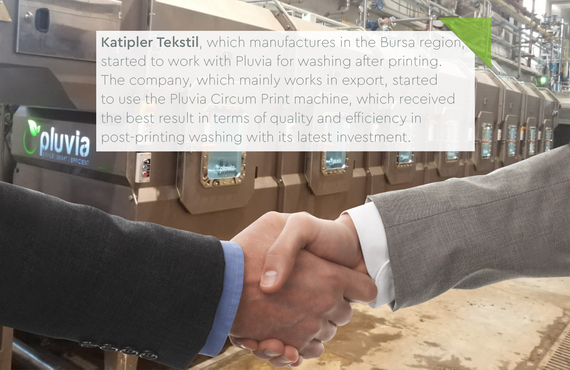
Consumption of textile materials is gradually increasing due to the growth in world population, improvement in quality of life and inclusion of fashion industry on diversity. The worldwide pressure on environmental issues is also steadily increasing, thus making sustainable production practices a necessity.
When considering the sustainability in textile industry, high water and energy consumption and the resultant waste emissions are the biggest obstacles in sustainable production. Within the textile industry, textile finishing is one of the most water intensive sub-sector due to high amount of water consumption in wet processes such as pre-treatment, dyeing and washing. Over the last few decades, many textile finishing machines have been developed with low liquor ratio to reduce overall consumption.
Hence, due to both environmental considerations and cost factors, efforts have been made for minimization of water consumption. Specific water consumption in textile finishing mills varies between 25 L/kg and 200 l/kg, depending on the type of material and process used¹. Achievable minimum specific water consumption levels were reported by European IPPC (Integrated Pollution Prevention and Control) Bureau² as 70-120 L/kg for yarn and knitted fabric finishing, and 50-100 L/kg (< 200 L/kg for some cases) for woven fabric finishing. However, more than 200 L/kg (even more than 600 L/kg) specific water consumption values have also been reported.
This reveals that reducing water consumption is now an imperative for dye houses due to both environmental and cost effects. International fashion brands are also forced to produce in the environmentally friendly and shortest and most efficient method and increasing price competitions make it necessary to find the right solution for this problem at once.
Washing in the dyeing machine causes much more water consumption than the main process, dyeing. In addition, due to the discontinuity of the process, the only action that can be taken to catch fastness results is to increase the number of baths. This inevitably increases water, energy, chemicals and time consumption.
An idea put forward by Pluvia in 2010 is now accepted by the leading dye houses all over the world and is seen as the most efficient solution to this problem. Pluvia washing machines offers a solution at this point. As soon as the dyeing process is finished, you can take the fabric out of the dyeing machine and take it to the continuous washing process in the Pluvia Circum machine. Since the machine operates in rope form, no intermediate process is required. Thus, you can make the washing process much more efficient by removing it from the jet dye machine that is not designed for this job. In this way, the capacity of the dyeing machine will increase by 40% and its main job will only be dyeing.
As a result of effective washing with Pluvia, the fastness quality increases with very low water consumption of 8-12 l/kg.
The results obtained from the dyehouses that use this idea for a dark shaded reactive dyed cotton fabric are as follows:
For more detailed information on the subject, you can contact Pluvia from the website and contact addresses below.
1) Maria L.C. Alves, Leao C. P., Sustainable work environment with lean production in textile and garment industry.
2) Tekstil Sanayii İçin En Uygun Teknikler (BAT ) Referans Dökümanı ( Türkiye Tekstil Sanayicileri Birliği )